When shopping for a SWIR camera, users often ask themselves whether or not they need a cooled camera and if they do, how much cooling do they need? One may be anxious about the idea of using an uncooled SWIR camera while someone else might worry about power requirement, heat dissipation or other consequences arising from cooling. Understanding the effects of temperature on performance, form factor etc is critical to making the right decision when it comes to selecting a SWIR camera.
How does temperature affect quantum efficiency of an InGaAs camera?
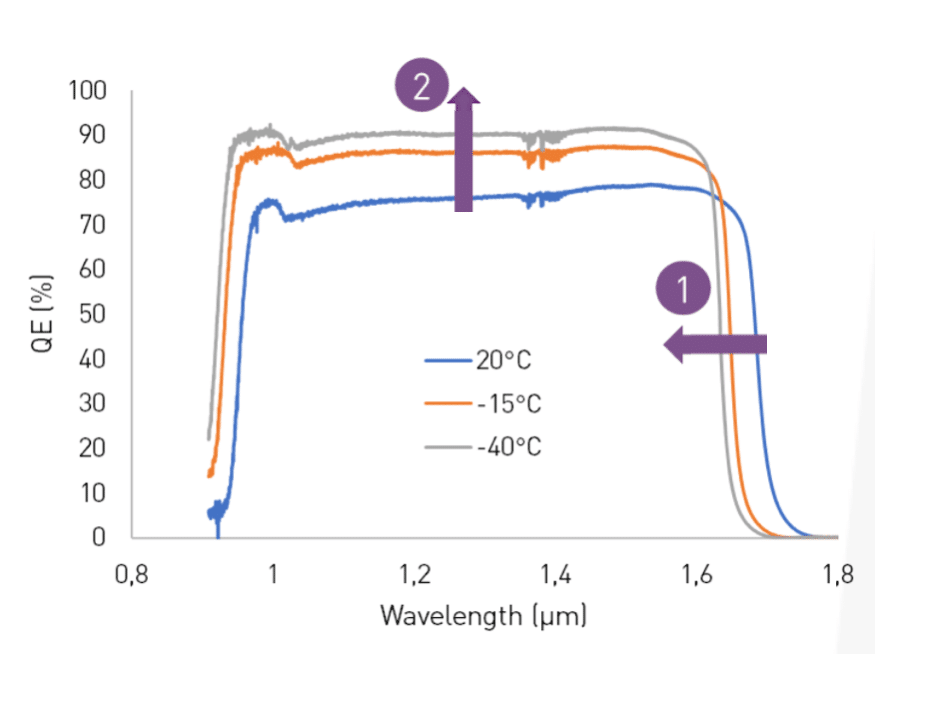
The figure on the left illustrates the quantum efficiency (QE) of a typical InGaAs FPA versus wavelength and operating temperature. Two things simultaneously happen as temperature decreases:
- the curve shifts towards the blue. This shift can be calculated to be ~ 1 nm every 2ºC.
- the peak QE increases by ~ 1% every 2ºC
This phenomenon is often not mentioned and can sometimes affect the performance of the camera depending on the application. One can think of someone working on the edge of the curve where cooling too much might mean losing 50% if not more of the QE.
Take away message: when looking at a QE curve for InGaAs, it is important to know which temperature it is alid for.
How does temperature affect the dynamic range of an InGaAs camera?
The useful dynamic range of a camera is the part of the integrating capacity available for photons. This dynamic range is limited by the dark signal, which is caused by thermally generated electrons in the sensor or dark current. The dark signal increases linearly with the exposure time and exponentially with temperature until saturation of the sensor (defined by the full well capacity). The figure on the right shows how the useful dynamic of an InGaAs camera is reduced as a function of exposure time and temperature.
Take away message: the useful dynamic range of a camera depends on the full well capacity and on the level of dark signal.
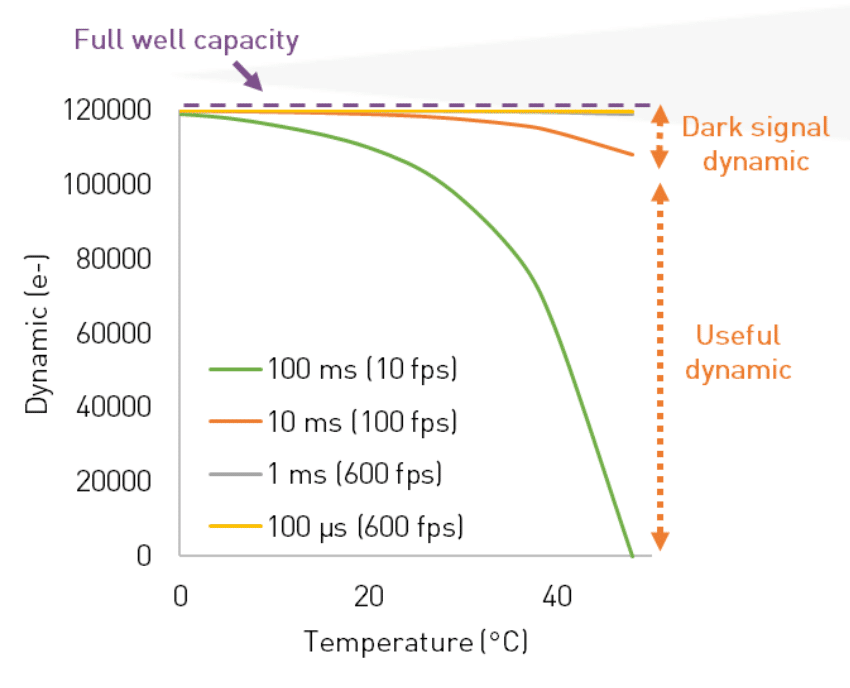
How does temperature affect the total noise of an InGaAs camera?
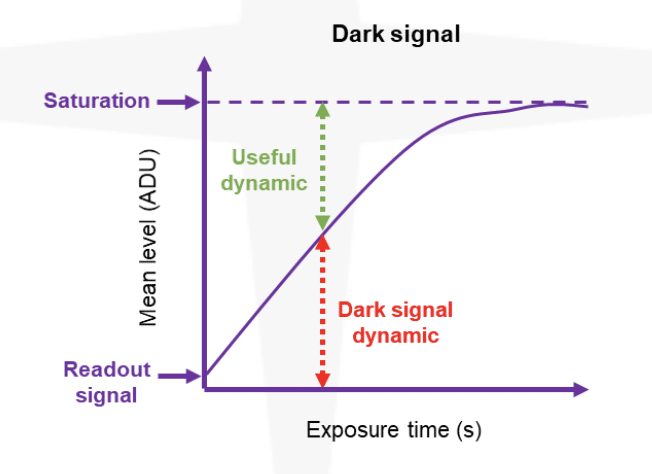
When looking at the noise specifications of an InGaAs camera (or any other camera really), there are two main sources of noise to consider:
- The dark current noise (caused by thermally generated electrons in the sensor) is equal to the square root of the dark current signal. Therefore, the dark current noise is a function of exposure time and temperature.
- The readout noise (sometimes referred to in data sheets as temporal dark noise). It is the noise created when the electrons are subjected to the analog to digital conversion, amplification and processing steps that enable an image to be produced.
Take away messages:
- the dark current noise adds to the actual readout noise. As the exposure time is increased, the dark signal increases linearly until saturation of the pixels.
- Pixels exhibit an exponential dark current increase with temperature, generally doubling every 7 to 8°C.
The figure on the right illustrates how the total noise varies in function of exposure time and temperature.
Take away messages:
- for short exposure times, the dark current noise contribution can be considered negligible. The camera is ‘readout noise limited’
- as the exposure time increases, the dark signal contribution increases and eats away at the useful dynamic range. How much is acceptable depends on the application and the dark signal contribution can be mitigated by decreasing the sensor temperature
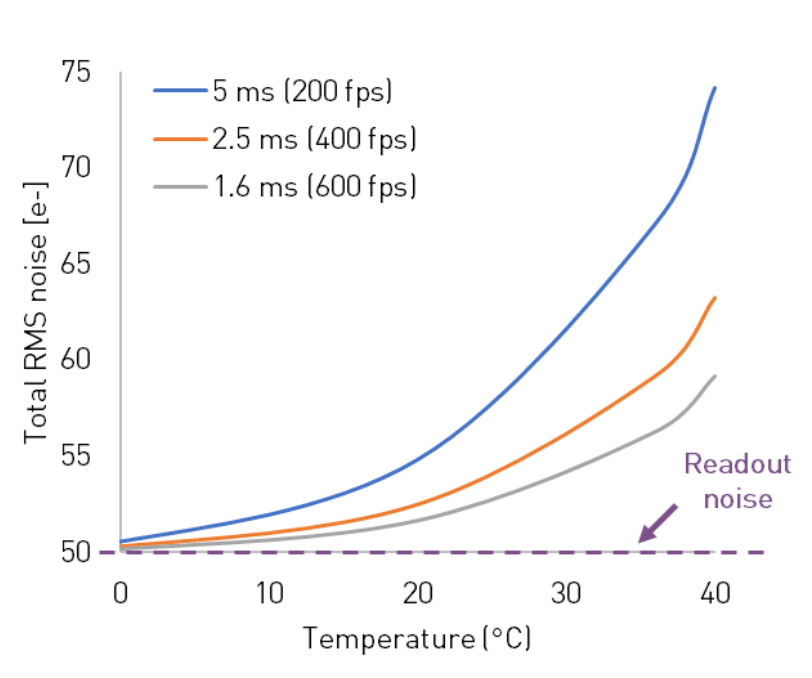
Cooling to stabilize
Cooling is used to decrease the sensor temperature set point with the purpose of optimizing the camera performance by reducing the level of dark current noise and thus allowing for longer exposure times.
In many applications, cooling for the sake of cooling is not necessary. Without any cooling, the sensor temperature will rise and reach an equilibrium given the environment temperature. Stabilizing the sensor consists of cooling the sensor to maintain the it at a defined temperature set point with limited fluctuations in time. It is achieved by cooling or heating the sensor with a retro-active feedback. The purpose is to achieve a perfect control over the camera response despite the variations of the environment temperature, thus insuring reproducible results where quantitative measurements are necessary.
It is therefore important to scale the level of cooling necessary to the requirements of the application. Stabilizing the sensor does not necessarily mean cooling it below room temperature!
How much cooling do I need? Let’s review some scenarios.
- The first question to ask ourselves is whether or not the application requires quantitative data that must be reliable and consistent day after day over a long period of time. If that is not the case and the level of photons available is sufficient to produce a good SNR, cooling might not be necessary. This is typically the case for qualitative imaging where the analysis is based on contrast difference or change over time.
- For quantitative measurements where the pixel intensity must remain stable over time to insure repeatability and reliability, a simple thermo-electric cooling 1 stage should be used. This is typically the case for applications such as laser beam profiling, hyper spectral imaging etc where data is collected and variations of the raw signal over time is unwanted.
- The application is such that you are photon starved. This the case when the signal to measure is so small it is buried in environmental noise or background noise. To reach a level of signal to noise ratio allowing for the detection of the signal, a longer integration time is necessary. Being able to reduce the dark current to a minimum is critical and can be achieved by having a larger cooling capacity.
Solutions include:
- A stronger thermoelectric cooling (multiple TE cooling added back to back or in ‘stages’). We are then talking of a TEC-2 or even sometimes TEC-3 or TEC-4.
- Using an airflow from an electric fan to create a forced convection. Often times this is used in conjunction with a TE cooling to help dissipate the heat generated from the hot plate.
- Waterflow, which induces a forced convection effect; the cooler the water is, the more efficient the heat dissipation is. Flow can be generated with a passive device or with a chiller device which will actively cool down the water
Look for the cooling power or “delta T” to know how much cooling can be achieved with your camera.